Autonomous Agriculture Machines One Step Forward in Next-Gen Farming
In the ever-evolving landscape of agriculture, the introduction of autonomous AG machines is seen as a solution to tackle a major concern, feed the world in a more sustainable way. Autonomous operation requires that the machine be precise and dependable. It must also preserve the farmer’s assets and the environment. Ensuring productivity means optimizing operating times and reducing maintenance.
Autonomous Agriculture Robots in the Wine Industry
Autonomous agriculture robots are designed to perform various tasks traditionally handled by skilled human labor on conventional machinery. These tasks include planting, weeding, treatment, harvesting, and even monitoring crop health.
Avoiding obstacles is critical for safety. Robotic start-ups and companies have been working for many years on visualization, real-time kinematic positioning systems and probing solutions to detect real or fake obstacles.
They were the early adopters of innovative technologies like Artificial Intelligence and machine learning. Autonomous robot OEMs can rely on Poclain’s proven propel solutions. The integration of hydrostatic drive systems in autonomous agriculture robots is showing promising results. In vineyards, they enable to navigate tight rows and steep slopes and perform the tasks that enable vineyards to thrive.
Poclain’s Solution, the Wheel Drive Motor
In row crop farming, the high torque density and compact envelope of the Poclain wheel drive motors are a strong asset. The robust hydrostatic wheels can operate in a harsh environment, offering high resilience to shock and vibrations. Poclain wheel motors can easily adapt to different terrain types, whether it is soft soil, mud, or uneven ground. Their parking brakes require minimal energy to maintain the brake released. In the event of a lack of energy, the brakes will automatically engage to stop the machine.
Direct hydrostatic drive motor is smooth and precise, ensuring accurate navigation and travel speed. Rugged speed and direction sensors located inside the motor provide speed and navigation feedback.
The direct drive solution is also gearless, so maintenance is limited to changing the transmission fluid and replacing the filter. No additional lubricant is needed.
Poclain Pairs up with Pioneers
Exxact Robotics, subsidiary of Exel Industries, and their TRAXX machine are a notable example of the use of Poclain MS02 wheel motors and PM10 pumps on autonomous robots in precision farming.

The robot helps winegrowers by minimizing the use of fungicides, herbicides, and insecticides, while also implementing agronomic strategies to combat biological pests. For its robot, Exxact chose the wheel drive solution, a proven technology on conventional straddle tractors. The new diesel machine can run up to 35 hours with a mileage consumption as low as 3 liters per hour.
Yanmar decided to take advantage of the high-power density from the Poclain MK04 motors and PM10 pumps for their track driven straddle robot. The YV01 machine was designed with the operator’s health and soil preservation in mind. The 25 HP ICE engine machine is used for spraying. The result is an autonomous machine that can drive up to 4 kph and climb a 45% slope and a lateral slope of up to 20%. The machine can be transported on a 3.5-ton trailer.
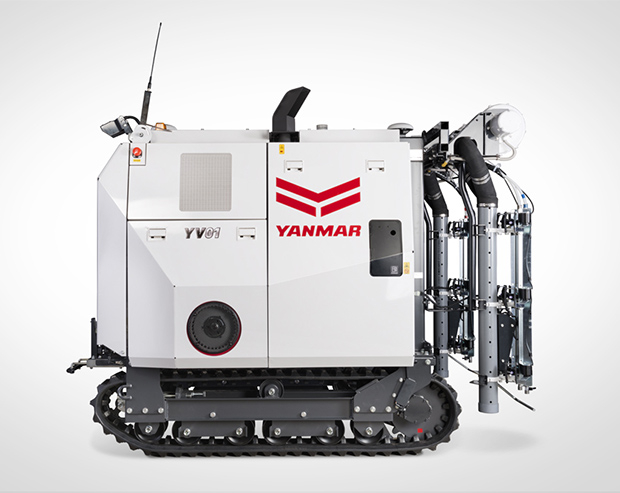
Future Outlook
Real autonomy will provide a ground breaking change in farming. One of the limits curbing the adoption of autonomous Ag machines is that they cannot currently operate without the direct supervision of an operator. Looking forward, the future (EU) 2023/1230 Machine Regulation should allow this, under the condition that a supervisory function be available with the possibility to trigger an override in real time. The second important limit is the need for higher productivity. Autonomous machines need to operate at higher speeds with fewer stops. Visualization tools, mostly based on AI systems are the culprit. They are still not trustworthy enough for safety functions. So machines need to detect obstacles by probing them at a reduced speed which cannot be over 2.16 kph (0.6 m/s).
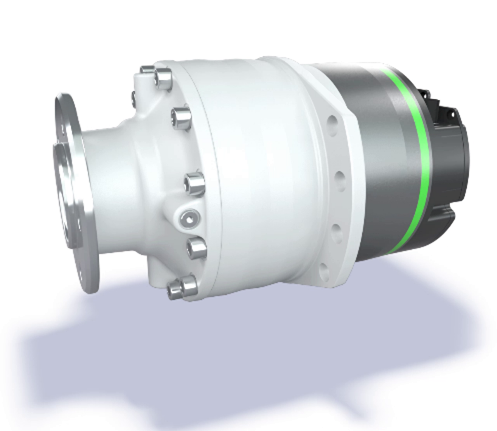
Nevertheless, the adoption of the autonomous solution is likely to increase as farmers and authorities recognize the benefits of reduced labor costs, increased efficiency, and sustainable practices. Poclain is committed to supporting the shift to autonomous technology by providing a range of advanced wheel drive solutions for propel systems. At the 2025 Bauma Munich exhibition, Poclain is presenting the next level of our technology with eWheels that can provide full electric propel drive, starting with a range of around 2000 Nm.
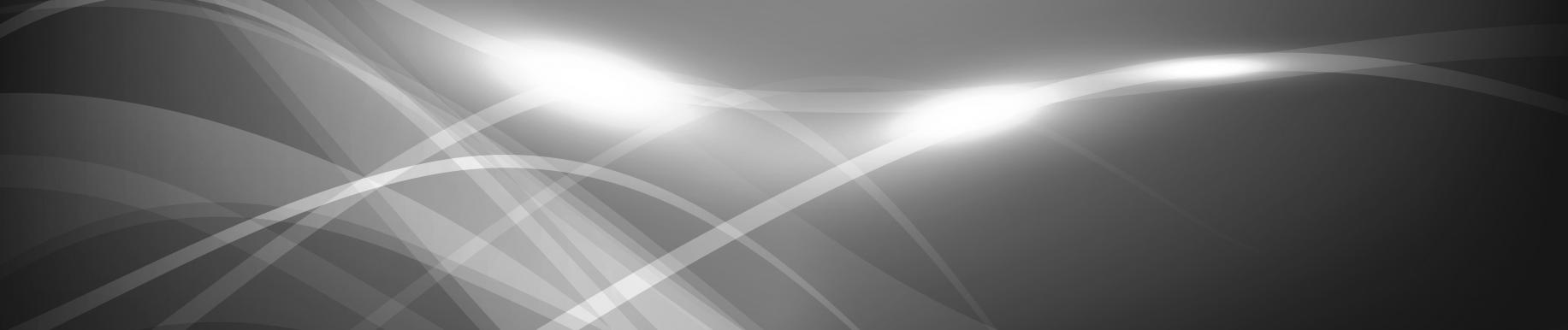