ELECTRO-HYDRAULICS FOR OPTIMAL E-VEHICLE PERFORMANCE
E-powered off-highway applications have been around for a while, in applications that give top priority to clean air and low noise levels. Electric motors can for example be found on mining vehicles, plastic injection machines and industrial forklift trucks. Other machines, such as truck-mounted forklift trucks, cannot integrate heavy batteries into their light structure; high gradeability and torque at low speed, which are paramount on loaders and excavators, are another obstacle. Today’s batteries have progressed in performance, size, and cost, thus opening new perspectives on high volume machines.
Recover energy with electro-hydraulic solutions
The technology of Poclain Hydraulics motors has been perfected with each upgrade, and today’s MHP, the fifth generation, is the most efficient and power-dense. The radial piston technology delivers high efficiency, rated at minimum 93%, across the entire motor range, and offers multiple displacements, smooth changes in the direction of rotation, as well as zero-drag freewheeling.
A closer study of how electric and hydraulic motors perform shows that they work in unison, in forward as well as in reverse, and can equally accelerate and decelerate the vehicle. When working together, they will enable batteries to work longer hours on the job site:
Forward drive and acceleration (quadrant I in the chart): both the electric and hydraulic motors function at optimal efficiency.
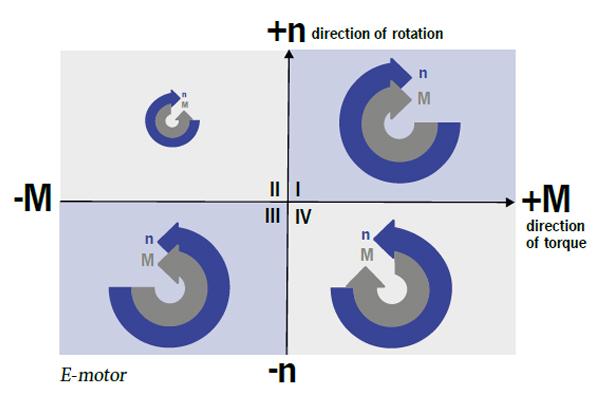
Forward drive and acceleration (quadrant I in the chart): both the electric and hydraulic motors function at optimal efficiency.
Forward drive and deceleration (quadrant II on the chart): hydraulic and electric motors also perform at optimal efficiency. The driver has high control over the machine, whether on a flat terrain or when going downhill. Electric motor deceleration also enables the brakes to last longer. And we can go one step further: as the driver decelerates, the hydraulic motor powering the wheel acts as a pump, the pump as a motor, and the electric motor as a generator, feeding the battery with the energy it has recovered.
Reverse drive (quadrants III and IV): the electric and hydraulic motors offer the same performance levels.
In an IC and hydraulic motor configuration, the performance levels vary:
The IC engine, in comparison, cannot operate in the opposite direction when the vehicle drives in reverse (quadrants III and IV); in addition, it has limited deceleration capabilities (quadrant II). The driver has to use the brakes to counteract the vehicle inertia.
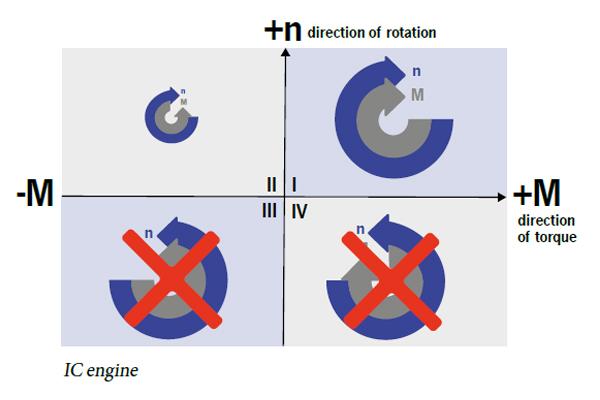
Electro-hydraulic versus pure electric
An all-electric vehicle comprised of an electric motor coupled to a fixed ratio axle does not offer a variable transmission ratio; the ratio between the electric power source and the electric motor driving the wheels is constant. This means you cannot choose the torque and speed levels required from the electric components for a given power level. When driving up a 25% grade, the driver does not have the capacity to shift into a lower gear.
An electro-hydraulic transmission, which comprises an electric motor for propulsion, a variable displacement pump with electronic control and hydraulic motors in the wheels, enables to adjust the transmission ratio on-the-fly. The pump swashplate angle adjusts itself to combine the most efficient combination of electric motor and hydrostatics at the required flow and pressure. As a result, the electric motor current decreases, less heat is generated in the motor and battery autonomy increases.
Electro-hydraulics applied to slew drives and grape harvesters
If you take the example of an excavator, shifting from an open-loop to a closed-loop hydraulic circuit slew drive allows for energy recovery when the turret slows down. The energy can be transferred to other functions in real-time, and/or stored thanks to ultra-capacitors or hydraulic accumulators, both of which can withstand large power peaks. Performances and operating range are enhanced.
Likewise, an off-road vehicle, which mostly operates on a grade such as a grape harvester, can integrate a hybrid engine with the electric motor taking over in the downhill working mode. The operator has more control over his machine and the energy recovered in the battery can be utilized to boost the engine when extra power is required. The OEM can downsize the IC engine, given that the power requirement with a hybrid solution capable of energy recovery is lower, and the operator will save on fuel.